Vacuum furnaces process hard zinc and recover zinc metal. The normal working conditions of the vacuum distillation furnace are the vacuum degree of 500~2000Pa and the temperature of 950~1050℃. Under this condition, the vapor pressure of the graphite electrode is very low, and its volatilization loss is negligible, so its service life depends on its degree of oxidation and fracture caused by mechanical and electrical failures. Specifically, what are the reasons for the loss of graphite electrodes in vacuum furnaces?
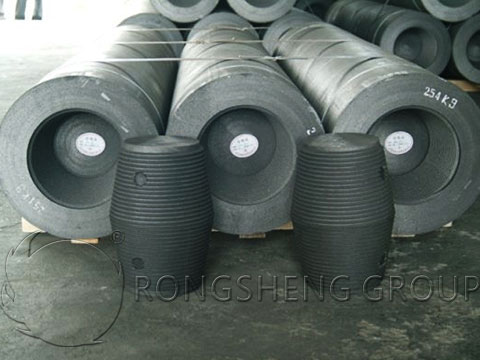
Oxidation loss of graphite
The oxidation of graphite is divided into dry oxidation (air, water, carbon dioxide gas) and wet oxidation (acid, alkali). Graphite is easily oxidized by air, water and carbon dioxide gas (CO2) at high temperature to form carbon monoxide or carbon dioxide. The product of its oxidation varies with the ambient temperature.
2C + O2 = 2CO (above 1 000°C)
C + O2 = CO2 (below 1000℃)
Graphite oxidation products are easy to escape and cannot form a dense oxide film protective layer like on some metal surfaces, so the oxidation reaction is continuous. The temperature and reaction speed at which graphite starts to oxidize are different in various cases. If the temperature at which 1% of the original weight is lost within 24 hours is set as the oxidation start temperature, the oxidation starts temperature of graphite is as follows.
-
-
- In air: 420 ~ 460 ℃;
- In carbon dioxide gas: about 900 °C;
- In water vapor: about 700°C.
-
Generally speaking, graphite with a large porosity, especially a large open porosity, has a large surface area participating in the reaction, and of course the oxidation rate is also fast. The higher the degree of graphitization of graphite products, the better the oxidation resistance. The aggregate of graphite products also has an important influence on oxidation resistance. Graphite products made of aggregates such as petroleum coke and natural graphite with good graphitization properties have excellent oxidation resistance. The presence of trace metal impurities will obviously promote the dry oxidation of graphite.
In the production process of graphite, metals that are usually easy to exist in the form of impurities include sodium, potassium, magnesium, calcium, iron, vanadium, copper aluminum, titanium, etc. Among them, the existence of sodium, potassium, vanadium and copper can catalyze the oxidation reaction of graphite. As the oxidation reaction proceeds, these metal impurity particles move through the material and form defects or pores. This phenomenon is more obvious in the oxidation reaction at lower temperature. According to the data, when some metal impurities are artificially added, such as adding 20 ~ 40μg/g of sodium, potassium, vanadium or copper, the oxidation rate at 550 °C can be increased by 5 times.
Electrode short circuit or crushed
The vacuum furnace uses graphite electrodes as heating elements, and requires good contact between electrode components during installation. Keep the vertical direction horizontal, and reserve an expansion gap around the installation window at the end of the electrode nut. At the same time, both ends of the electrode assembly and the furnace shell maintain good insulation performance. Due to the poor sealing of the installation window, the zinc vapor in the feeding trolley enters the electrode nut or the electrode connection card through the gap of the sealing material, and condenses into a zinc block. With the continuous growth of the condensed zinc block, it will eventually contact with the iron shell of the furnace body, causing the electrode to short-circuit and damage the electrode. After the furnace shell and electrode support plate are deformed, the expansion gap at the end of the graphite electrode nut is usually insufficient. After the power is heated up, the electrode nut is squeezed by the furnace wall around the installation window to varying degrees, and the electrode is quickly broken.
Electrode processing quality, installation quality
The electrode processing quality and installation quality also have a very important influence on the service life of the electrode. The connection thread of the electrode and the electrode nipple is poorly processed or the tolerance matching does not meet the standard, which will cause the connection between the electrode and the joint to be too loose or too tight. Too loose will cause poor contact and arcing will burn the electrodes and nipples; too tight will easily damage the threads during assembly. When assembling the electrode, during the screwing process of the electrode and the electrode joint, the action is rude, which will also cause damage to the thread and cause the electrode to be scrapped.
In addition, when the water-cooled electrode is short of water, the heat of the electrode connection card cannot be taken away in time. It will also cause poor contact between the electrode and the card board, thereby burning the electrode connection card board. In severe cases, arcing will burn the electrode and the electrode connection card.
It can be seen that the graphite electrode is still easily worn out in the process of use. Therefore, it is helpful to purchase high-quality graphite electrode products and standardize the operation and installation procedures to reduce the loss of graphite electrodes.