At present, in electric arc steelmaking, as the discharge power and electrode diameter increase, the heat generated by the working current will increase rapidly, and the requirements for joint connection will be more stringent. To realize the ideal connection of the electrode, in addition to improving the processing quality of the joint and the joint hole, and improving the joint material, there are also appropriate requirements for the tightening torque. Make the pre-tightening force appropriate to avoid too much pre-tightening force causing breakage from the joint during work. Or the pre-tightening force is too small, causing the electrode to fall off during work.
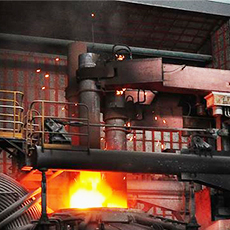
The Relationship between “Skin Effect” and Electrode Connection
When direct current passes through a conductor, the current in the cross-section of the conductor is uniform. When an alternating current passes through the conductor, the current will concentrate on the surface of the conductor. This phenomenon is called the skin effect of alternating current. The higher the frequency of the current, the more obvious the skin effect. The extent to which the current leaves the center of the conductor section and concentrates on the surface can be expressed by the depth of the skin effect.
The expression of the skin effect depth is:

In the formula, f is the frequency of the alternating current, in Hz; k is a constant, which is related to the resistivity of the conductor.
It can be seen from formula (1) that the depth of the skin effect decreases as the current frequency increases.
Due to the skin effect, when the electrode is working, under normal circumstances, about 80% of the current flows through the annular belt between the electrode joint and the outer surface, and about 20% of the current flows through the central electrode joint part. This is undoubtedly beneficial to the electrode connection. If the end faces can fit well when the electrodes are connected, the skin effect will be fully utilized, so that most of the current flows through the outer loop. Reduce the resistance heat of the joint part and avoid burning and breaking due to heat. At the same time, the good fit also makes the contact resistance very small and reduces the power consumption.
From the above, in order to make full use of the skin effect, when connecting the electrodes, it is necessary to make the end faces fit as much as possible. At the same time, when the electrode is in discharge, the connection between the electrode and the connector is easily loosened due to electromagnetic vibration. Therefore, it is necessary to apply pretension.
When the electrode connection threaded hole is processed, there are strict requirements on the perpendicularity of the end face to the thread axis, and the end face should be concave by 0.05~0.1mm, which needs to be determined according to the elastic modulus of the electrode material. The ideal connection state of the electrode is to apply an appropriate pre-tightening force to make the end face elastically compressed and deform, overcome the concave, and achieve full fit. At the same time, it is necessary to control the size of the pre-tightening force. It cannot be too big or too small. If the yield strength of the joint is exceeded, failure fracture occurs. The pre-tightening force is small, and it cannot provide enough positive pressure and friction between the threads, causing looseness.