The physical performance requirements of large-scale, UHP graphite electrodes, with the introduction and continuous expansion of DC electric arc furnaces in my country, are of great significance for the best use of electric arc furnaces and reducing electrode consumption. Therefore, in order to promote the development of the electric furnace steelmaking industry, it is also extremely necessary for the development of large-scale, ultra-high power electrodes. Next, we will learn more about the application and cost-saving of graphite electrodes in electric arc furnaces from two aspects: the best use conditions of the electrodes in the DC arc and the physical properties of large-size graphite electrodes for DC electric arc furnaces.
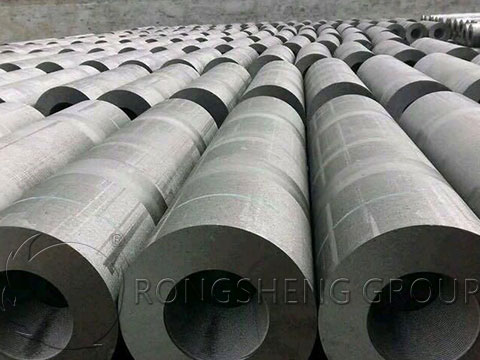
The Best Use Conditions of Electrodes in DC Electric Furnace
A certain electrode diameter corresponds to the best current load. Only in this way can the consumption of the electrode be the lowest, the utilization rate is the highest, and the role of the electrode can be fully and effectively played. H. Hagd et al. proposed two calculation criteria for a certain electrode diameter corresponding to the maximum current load. The first criterion is to calculate the current load capacity by considering only the thermal load; the second criterion is to calculate the current load capacity by calculating the mechanical stress through the thermal load.
Figure 5 shows the maximum tangential tensile stress of the φ600mm electrode at different current intensities. The calculation takes into account the conical shape of the electrode tip. The experimental results show that the maximum current load of the φ600mm electrode is about 85kA, and the maximum tangential tensile stress value generated at this time is 22MPa. When the current load is 62kA, the maximum tangential tensile stress on the outer surface of the electrode at the connection is 11.2MPa. This value is the lowest current intensity value at which the connection is broken, the electrode is peeled off, and the crack grows.
Fig. 6 is the upper limit of the current load corresponding to a certain diameter electrode obtained according to the thermal interception load (first criterion). Fig. 7 is the upper limit of the current load corresponding to a certain straight electrode obtained by calculating the mechanical stress (the second criterion) through the thermal load. Comparing the current load limit values obtained by the two criteria, the results are relatively consistent and satisfy the linear relationship. In practical applications, the second criterion is more important when the results obtained are applied to electric furnace electrodes. Because the second criterion is the result derived from thermal stress, and thermal stress is often one of the important reasons for electrode failure and connection damage.
The performance of graphite electrodes and nipples produced in my country is definitely different from that of H.Hagel calculation electrodes. Therefore, our application of this criterion can only use its linear relationship, and the general trend should be consistent.
Physical Properties of Large-Size Graphite Electrodes for DC Electric Solitary Furnace
With the increasing number of high-power and large-capacity DC electric furnaces, the electrode diameter is getting larger and larger, up to φ800mm, and the current interception is getting higher and higher, reaching 150kA. It is very important to choose a suitable electrode quality standard to meet the needs of high-power and large-capacity electric furnaces. All practical and theoretical studies have obtained the same results, and the performance of large-scale graphite electrodes needs to be improved even more. This requires attention to the selection of raw materials and the establishment of advanced production processes.
Higher requirements are put forward on the physical properties of large-size electrodes used in DC electric arc furnaces.
(1) The resistivity is further reduced. In this way, the power loss (I2R) is small, and a reasonable temperature gradient can also be obtained. This requires a higher graphitization temperature to ensure a decrease in resistivity.
(2) The coefficient of thermal expansion should be low. Since the graphite electrode and the graphite electrode nipple at the connection site have different thermal expansion properties in the axial and radial directions, the temperature at the nipple is higher and the thermal stress is greater. Under the premise of low thermal expansion coefficient, the axial and radial thermal expansion coefficient of the electrode should be slightly greater than or equal to the nipple and should satisfy αpTp-αNTN ≥ 0. Among them, αp is the thermal expansion coefficient of the electrode; Tp is the temperature of the electrode; αN is the thermal expansion coefficient of the nipple; TN is the temperature of the nipple. In this way, the thermal stress value is reduced. To achieve this, there must be advanced technology, raw materials, and formula to ensure.
(3) The thermal conductivity should be high. The high thermal conductivity allows the electrode to dissipate heat quickly, and the radial temperature gradient is small, which is also beneficial to improve the thermal stress. The thermal conductivity should be above 200W/m·K.
(4) It must have a certain strength. The electrode must have a certain strength, and the strength of the nipple is higher than that of the electrode. Large-size electrodes have a large weight. In order to ensure a reasonable current flow, there should be a higher pressure on the connection end surface. If the strength is insufficient, the connection thread will be damaged, local cracks will occur prematurely, and the failure rate will be accelerated. At the same time, we also hope that the modulus of elasticity should be low, so that the thermal stress σ = EaT is also reduced. Therefore, both strength and elastic modulus should be considered. The strength can be improved through process control, selection of reasonable formulas and raw materials, and multiple dipping processes.
(5) The porosity should be low. For electrodes, excessive surface porosity will increase oxidation and increase electrode consumption. Porosity can be improved by the surface treatment process.