Inner string graphitization is a process in which the current directly passes through the furnace core composed of roasted products in series, and the roasted products are graphitized through the thermal effect of the current. In the process of graphitization and power transmission, the baked product is treated at a high temperature above 2400°C and finally transformed into a graphite product with better conductivity and oxidation resistance. Graphitization is an important production link in the production of ultra-high power graphite electrodes, and graphite electrode products are accompanied by a series of complex physical and chemical changes in the process. By analyzing the actual changes in products and the causes of abnormal conditions during graphitization and power transmission, it is helpful to better formulate and improve process parameters and improve the product quality of graphite electrodes.
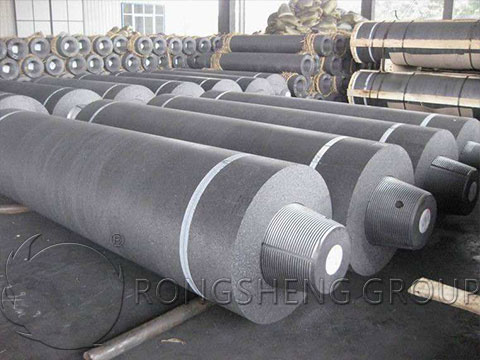
The graphitization process of a graphite electrode manufacturer uses a U-shaped inner series graphitization furnace. The products are loaded on the east and west sides of the furnace, and metallurgical coke is used as the furnace bottom material and insulation material. The joints for ultra-high power graphite electrodes are loaded into the graphitization furnace in a multi-column bundling manner. During the power transmission process, the displacement data of the product is determined by the expansion and contraction of the furnace tail-pushing equipment and is recorded and monitored by the computer. Through the summary analysis of various parameters before and after spraying the furnace in the inner string graphitization process of the joints for ultra-high power graphite electrodes. The physical and chemical changes in the graphitization process, the reasons for spraying furnaces, and the impact on product quality are explained, and corresponding solutions are proposed. It is hoped that it can promote the production of domestic large-scale ultra-high-power graphite electrode nipples.
Reason Analysis of Splattering of Lengthwise Graphitization
According to the production records, the graphite electrode nipple product was sprayed at time t6. The location of spraying furnace is located at the furnace head on the east side of the U-shaped graphitization furnace, and the maximum power transmission power has been reached when the furnace is sprayed. Before spraying the furnace, the furnace resistance increased abnormally. After spraying the furnace, re-energize and the furnace resistance returns to normal.
In addition to the length of raw materials and roasted products, the pusher device at the end of the furnace is also a factor affecting the displacement of the east and west sides. The pusher at the end of the furnace usually applies pressure to make the electrode series connection closely, so as to reduce the contact resistance between the electrode end faces. According to the research of the experimenters, the pressure should be adjusted in time during the graphitization and power transmission process to maintain a stable contact resistance. In addition, during the electrode inflation stage, the change of the pushing pressure on both sides of the furnace tail will also affect the displacement of the east and west sides to a certain extent.
In the actual power transmission process, the hydraulic pressure at the end of the furnace is controlled by the same hydraulic station. However, when there is partial blockage, oil leakage, or other problems in the hydraulic pipeline on one side, the actual acting pressure on the east and west sides may be different. This may be the reason for the difference in expansion between the east and west sides of ultra-high power graphite electrode products within a certain time interval.
As the temperature continues to rise, the graphite electrode product begins to shrink in the temperature range in the next period of time, and the amount of shrinkage gradually increases. At this time, according to the process requirements, the automatic hydraulic system at the end of the furnace needs to adjust the pressure in time to adapt to the shrinkage of the electrode string. However, when the hydraulic system at the end of the furnace fails to adjust the pressure quickly due to some reasons, and because the hydraulic device is located at the end of the furnace, it is far away from the furnace head. Affected by the frictional resistance of metallurgical coke, the pressure at the furnace head is lagging or insufficient, which is particularly likely to cause an increase in the contact resistance of the electrode end surface at the furnace head. Even in severe cases, the metallurgical coke insulation material enters the gap of the electrode end face. This leads to an abnormal increase in local contact resistance, resulting in burnout. This is also the reason why the graphitization spray furnace usually occurs at the furnace head.
Influence of Splattering of Lengthwise Graphitization on UHP Graphite Electrodes
After the graphite electrode nipple products are released from the furnace, through the analysis of the processing results, the qualification rate of the graphite electrode products on the east side of the graphitization furnace is slightly lower than that on the west side. This may be related to the larger displacement on the east side during graphitization and power transmission. In this temperature range, the chemical reaction is intensified, the stress is concentrated, and the excessive displacement will easily cause cracks in the product, resulting in unqualified products.
According to the normal distribution of bulk density and resistivity of processed graphite electrode nipples, the bulk density and resistivity of the east side are slightly lower than those of the west side. This may be related to insufficient push pressure on the middle east side during graphitization and power transmission and metallurgical coke entering the gap of the electrode end face. During the power transmission process, the contact resistance between the end faces of the electrode string on the east side is relatively high. According to Joule’s law, the east side generates more heat and has a higher degree of graphitization, so the resistivity and bulk density of the product decrease.
Solutions to Splattering of Lengthwise Graphitization
1) When graphitizing power transmission, the pushing pressure of the furnace tail should be adjusted appropriately according to the product diameter and furnace loading form. In order to avoid the situation that the furnace tail pressure cannot meet the production needs due to specification changes.
2) When graphitizing the furnace, small graphite blocks can be laid under the electrode trunk to reduce the influence of metallurgical coke friction resistance on the pushing pressure. There is hysteresis or insufficient pressure to improve the position of the furnace head.
3) The furnace tail pusher is one of the key pieces of equipment to ensure the normal power transmission of the inner string graphitization furnace. The change in its pressure is closely related to product quality, and it should be maintained and corrected regularly.
4) Graphitization During the power transmission process, the change of furnace resistance can timely and effectively reflect the real-time situation of the products in the furnace. It should be paid attention to during the power transmission process. When the furnace resistance is abnormal, the process can be adjusted in time to ensure product quality;
5) The graphitization power transmission is controlled by a computer program, and the pushing pressure can be considered to be added to the program. In order to realize real-time monitoring, and set relevant thresholds or alarm conditions for changes in furnace resistance.
Rongsheng Graphite Electrodes Manufacturer
Rongsheng graphite electrode manufacturer is an experienced manufacturer of graphite electrodes. Our graphite electrode customers continue to return orders from our manufacturers. Moreover, we support the customization of graphite electrode products and can provide you with customized graphite electrode products according to your specific usage requirements. Contact us to buy high-quality ultra-high power graphite electrode products.