The role of the electrode is to conduct electricity and convert electrical energy into heat. Electrodes are divided into three types: carbon electrodes, graphite electrodes, and self-baking electrodes according to their use and production process. In submerged arc furnaces, self-baking electrodes are mainly used, but when producing ferroalloy products with lower carbon content, such as industrial silicon, graphite electrodes are required. So what are the differences among the self-baking electrodes, carbon electrodes, and graphite electrodes?
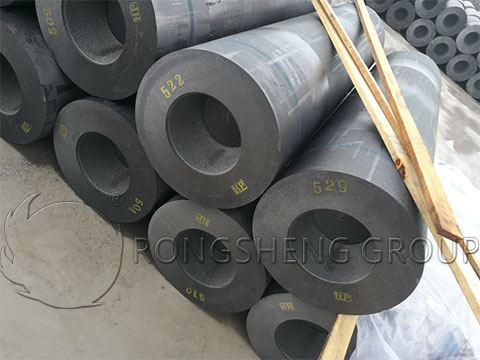
First of all, we must clearly distinguish these three electrodes.
- The carbon electrode is made of low-ash anthracite, metallurgical coke, pitch coke, and petroleum coke as raw materials, and is composed of a certain proportion and particle size. Add binder asphalt and tar when mixing, stir evenly at the proper temperature, and then press into shape. Finally, it is made by slow roasting in the roasting furnace.
- Graphite electrode uses petroleum coke and pitch coke as raw materials to make a carbon electrode. Then put it in a graphitized resistance furnace at a temperature of 2000-2500°C, and make it through graphitization.
- The self-baking electrode uses anthracite, coke, pitch, and tar as raw materials. The electrode paste is made at a certain temperature, and then the electrode paste is put into the electrode shell installed on the electric furnace. In the production process of the electric furnace, it relies on the Joule heat generated when the current passes through and the heat transfer in the furnace to self-sinter and coke. This kind of electrode can be used continuously, and sintered to form while connecting the long side, and can be fired into a large diameter.
The self-baking electrode has a simple manufacturing process and low cost and is widely used in ferroalloy production. It is usually used to produce ferrosilicon, silicon-chromium alloy, silicon-manganese alloy, high-carbon ferromanganese, low-carbon ferromanganese, high-carbon ferrochrome, low-carbon ferrochrome, silicon-calcium alloy, Ferro tungsten, etc. Self-baking electrodes are easy to increase the carbon of the alloy, and the iron skin of the electrode shell is also easy to bring the alloy into iron. Therefore, the production of iron alloys and pure metals with very low carbon content, such as micro-carbon ferrochrome, industrial silicon, silicon aluminum alloy, metal manganese, etc., uses carbon electrodes or graphite electrodes.
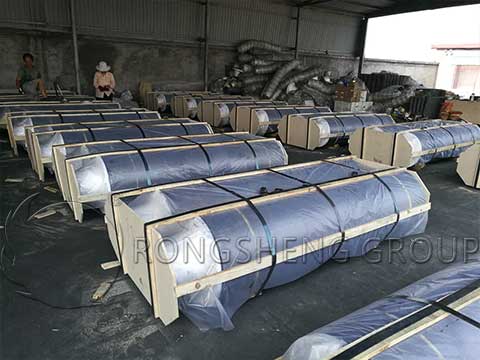
Graphite Electrodes Applications
Among them, graphite electrodes have excellent properties such as high temperature resistance, oxidation resistance, good electrical conductivity, high mechanical strength, low impurity content, and good thermal vibration resistance. Mainly used as electrode devices in electric arc furnaces and refining furnaces for smelting steel. Submerged electric furnace for producing ferroalloy, industrial silicon, yellow phosphorus, matte, calcium carbide, etc. Graphitization furnace for producing graphite electrodes, furnace for melting glass, electric furnace for producing silicon carbide, etc.
With economic development, the demand for refined steel has increased. Preparation of extruded large-size φ600~φ800mm high-quality GHP graphite electrodes, supporting the application of three-phase 6 and 9 or 12 power supply arrangements in a large ferroalloy submerged arc furnace smelting new technology method. Give full play to the high-quality characteristics of GHP graphite electrodes. Realize high-power, large-capacity, energy-saving and emission reduction, safe and efficient, low-cost smelting production in the ferroalloy submerged arc furnace industry, change the outdated technical level of ferroalloy submerged arc furnace smelting, and provide a new way for technological innovation, upgrading, and transformation of enterprises. Facilitate the virtuous cycle of green economy development.
Technical problems or product problems related to refractories and carbon materials for submerged arc furnaces. Please email us: info@graphelectrode.com.