Baking is an important process for producing uhp graphite electrodes with excellent performance. Factors such as heating rate, binder pitch, and temperature field have an impact on the quality of graphite electrodes during the baking process. It can provide a reference for the production of high-quality graphite electrodes.
Ultra-high Power Graphite Electrode
The ultra-high power graphite electrode has the advantages of low resistivity, good oxidation resistance, and a small thermal expansion coefficient. It is widely used in electric arc steelmaking furnaces with high current density and harsh working conditions. And its bulk density and flexural strength also need to reach a higher level. At the same time, its elastic modulus should be appropriate. It needs to match the performance of the matching electrode joints to show good thermal shock resistance during the electric furnace steelmaking process, and it is not easy to break. Therefore, it is necessary to strictly control the process parameters of each process of ultra-high power graphite electrode production to ensure that the product quality of each process is qualified and the internal structure of the product is uniform and stable. Therefore, continuously optimizing each link of process control is an effective means to obtain better quality products.
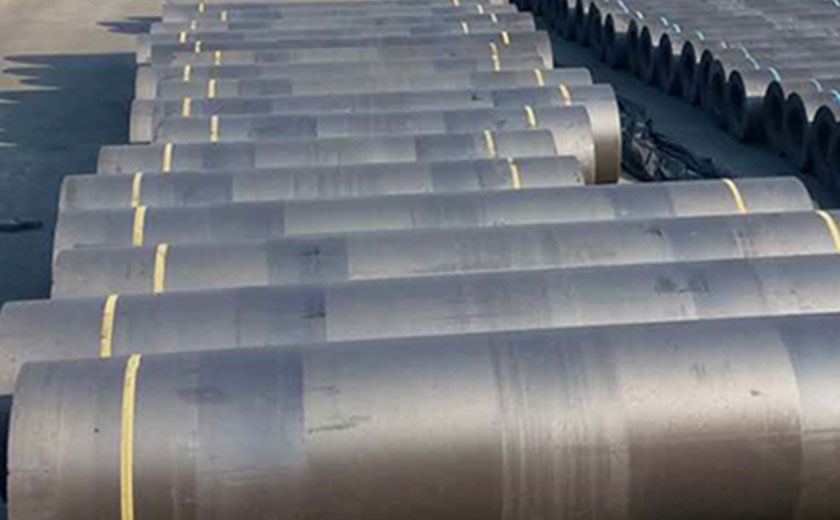
Mechanism Analysis of the Whole Process of Baking and Heating
Regarding the primary baking, no matter what baking furnace is selected, the heat generated after the fuel is burned is transferred to the refractory brick or the steel drum of the container baking. Then, the refractory bricks or steel drums are passed to the filler. Finally, the filler transfers heat to the raw product. Quality of Graphite Electrodes, When the temperature felt by the raw product itself exceeds the softening point of the binder pitch, the green body will first soften from the glass state and then become the molten state. Just under the squeeze of the surrounding filler, it keeps its original geometric shape.
On the one hand, with the gradual increase in temperature, the binder asphalt first undergoes physical lateral infiltration and longitudinal gravity migration. If the selected binder is medium temperature asphalt, its physical migration will be greater than that of the modified asphalt binder with a high softening point. Therefore, choosing high-temperature modified asphalt instead of medium-temperature asphalt as a binder is an effective measure to improve product quality. As the temperature continues to rise, the binder asphalt begins to decompose and polymerize. The discharge of light volatiles gradually increased. Heavy residues are also continuously polymerizing. The total volume of the raw product expands in the radial and longitudinal directions, while also shrinking. The practice has proved that the longitudinal expansion of the raw product is slightly greater than the radial expansion, so the mechanical strength of the upper end of the baked product is lower than that of the lower end. This is directly related to the migration of asphalt, and the choice of high-temperature modified asphalt binder can improve this situation.
On the other hand, the elasticity, air permeability, and adsorption of the filler also play a very important role in the firing process. Appropriately reducing the adsorption and air permeability of the filler, or adding refractory bricks on top of the insulating material will help increase the coking value of the asphalt binder. If the type of filler is determined, it depends on the particle size composition of the filler. If the filler is too fine, the discharge of volatiles from large-scale raw products will be too hindered, which will cause cracks in the product. Therefore, the adsorption and air permeability of the filler should be controlled within an appropriate range. When the radial expansion force of the product and the mechanical strength of the surface of the raw product reach a dynamic balance, the coking value can be maximized. Of course, this dynamic balance is closely related to the heating rate. In order to effectively improve the mechanical strength and density of the calcined product, it is necessary to ensure that the particle size composition of the filler matches the product specifications and heating rate reasonably.
The selection and control of the baking process are very important because it directly determines the structure, performance and production cycle of the final product. In the baking process, along with the transfer of chemical reaction and mass, heat and momentum, the three-phase system undergoes a series of continuous unequal temperature phase transitions, which makes the research of the system very complicated. In order to further clarify the baking mechanism, it is necessary to analyze the baking stages. Because there are obviously different phenomena in each stage of baking.